Introduction
Negative stiffness metamaterials are engineered to combine high stiffness with exceptional energy dissipation. By embedding inclusions into a host material. The inclusions amplify localized strain energy, enabling superior damping across static and dynamic conditions. Unlike resonance-based materials, NS metamaterials offer broadband damping, making them ideal for consilidating damping and structural components.
Theory
Micro-scale inclusions exhibit effectively negative stiffness behavior within a specific displacement range. In this range, the force-displacement curve shows a region where displacement increases without additional force, enabling significant local strain amplification. This behavior arises from the carefully designed geometry of the inclusions, i.e the elastically buckling curved beams.
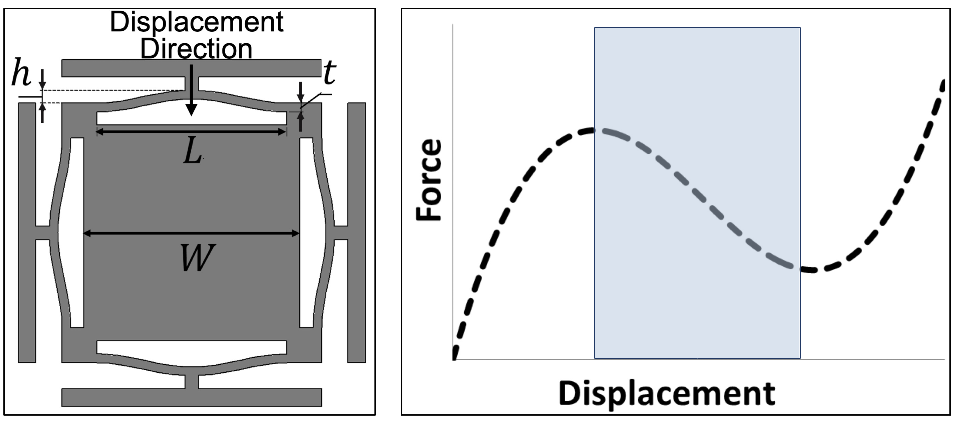
Force-displacement curve illustrating the negative stiffness region (blue).
By embedding these inclusions into a host material with complementary stiffness properties, the local strain amplification enables enhanced energy dissipation. The strain energy is localized to the negative stiffness regions of the inclusions, while the host material retains its original stiffness. This allows the metamaterial to dissipate energy effectively under dynamic and static loading, making it ideal for applications requiring both high stiffness and damping.
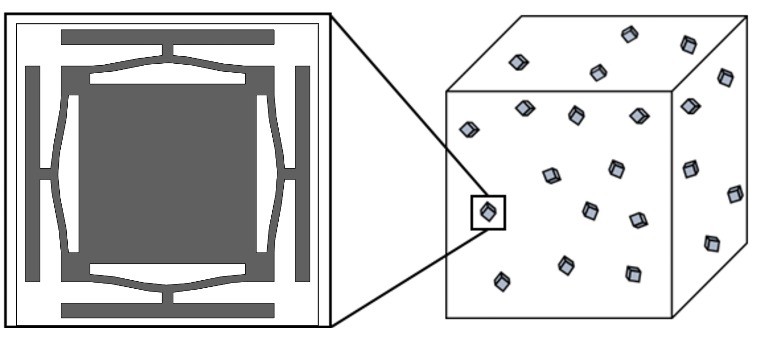
Embedded inclusions in the host material.
Hierarchical Nature of the Problem
Manufacturing NS metamaterials requires a hierarchical approach, integrating micro, meso, and macro scales seamlessly.
Micro-Scale
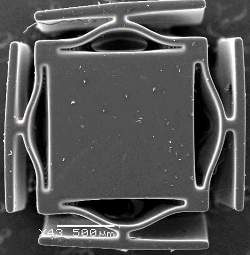
SEM Image of a NS Inclusion.
Meso-Scale
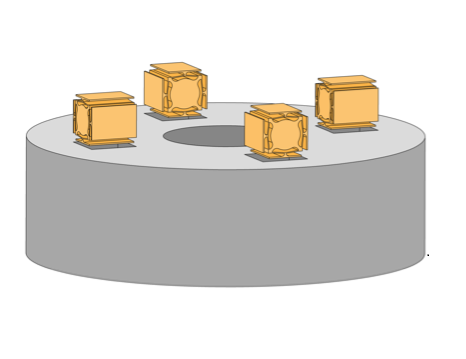
Embedding inclusions in a host matrix to achieve desired material properties.
Macro-Scale
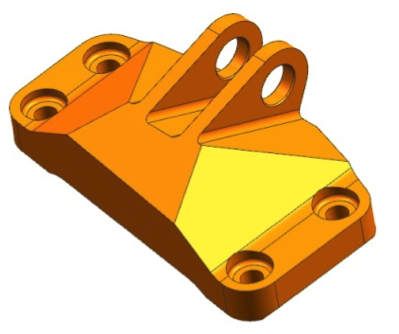
Structural components can be constructed from metamaterial.
Manufacturing Process
The manufacturing process for negative stiffness metamaterials involves two key stages: the precise fabrication of NS inclusions using microstereolithography and a multistep casting process to embed these inclusions into a polyurethane matrix. This process ensures that the metamaterial retains the unique properties of the inclusions while integrating seamlessly into the host material.
- Creating NS Inclusions:
Advanced microstereolithography is used to fabricate the NS inclusions, which are designed with precise geometric features. This additive manufacturing technique allows for sub-millimeter accuracy, ensuring that the inclusions exhibit the desired negative stiffness behavior. The process involves layer-by-layer curing of a photosensitive polymer resin under UV light, resulting in inclusions with fine details and consistent mechanical properties.
Microstereolithography system used to manufacture inclusion.
- Embedding in a Polymer Matrix:
The inclusions are embedded within a viscoelastic polyurethane matrix through a multistep casting process:
- Step 1: Base Layer Formation: A mold is prepared to create cavities that house the inclusions. The base layer of polyurethane is poured and allowed to partially cure, ensuring a stable foundation for the inclusions.
- Step 2: Inclusion Placement and Sealing: The NS inclusions are placed in the cavities, and a thin polyurethane film is bonded over them. This sealing step ensures that the top matrix layer does not intrude into the inclusion regions, preserving their elastic buckling behavior.
- Step 3: Final Layer Casting: A top layer of polyurethane is poured over the inclusions, embedding them fully within the matrix. The material is allowed to cure completely, resulting in a cohesive metamaterial with the inclusions securely aligned and distributed.
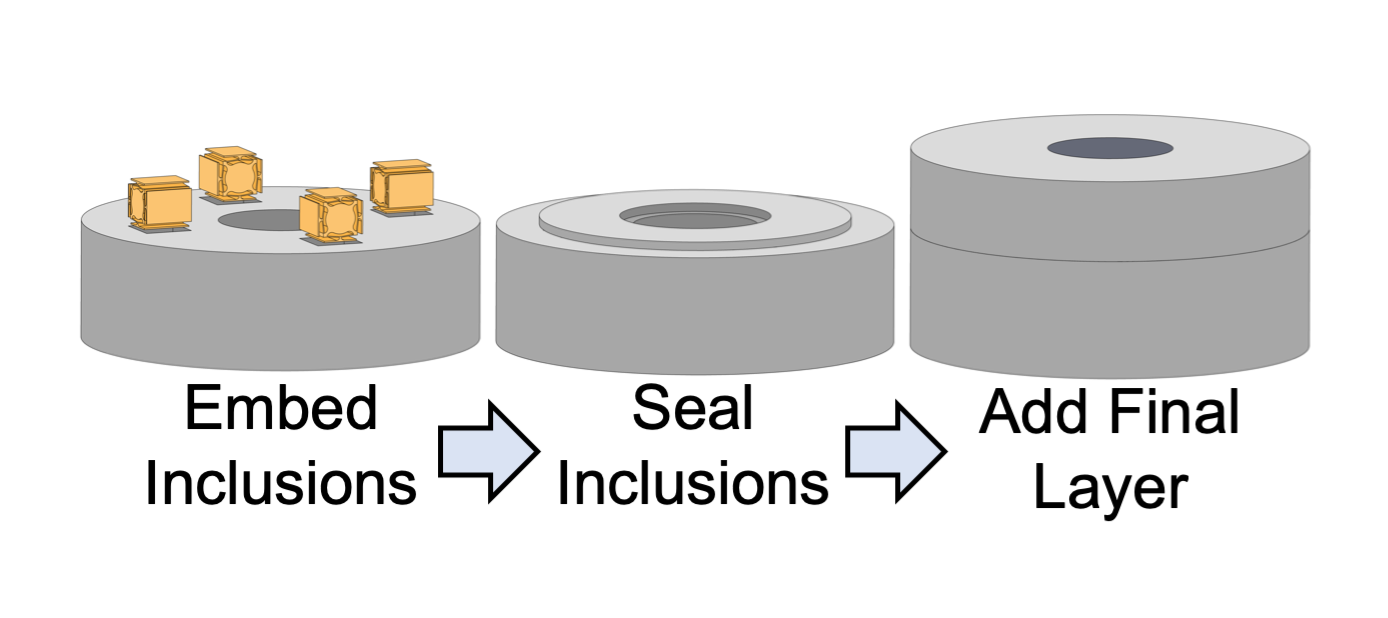
Manufacturing Process for NS Metamaterial
Testing and Validation
Static Testing
Static testing was conducted to evaluate the energy absorption and hysteretic behavior of the metamaterial under controlled, quasi-static compression. Three specimen types were tested: the control specimen, a voided specimen, and the negative stiffness (NS) metamaterial. Results showed that the NS metamaterial outperformed the other specimens, absorbing substantially more energy due to the strain amplification caused by the embedded inclusions.
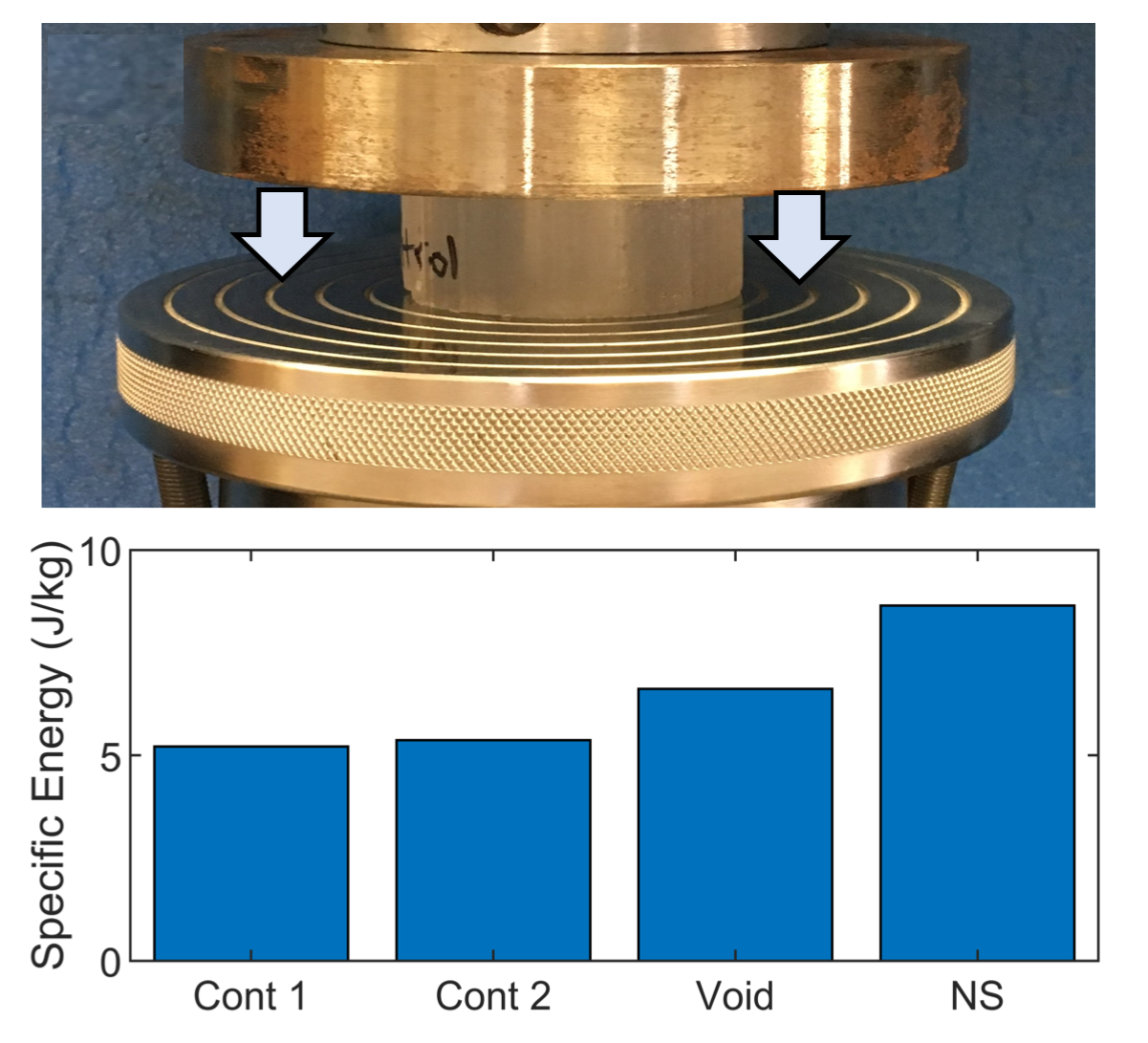
Dynamic Testing
Dynamic testing was conducted to assess the vibration damping performance of the NS metamaterial. A custom test rig was designed to apply precise levels of prestrain to the specimens, enabling controlled testing of transmissibility across various frequencies. The results revealed that at a specific pre-strain level, the NS metamaterial exhibited a marked increase in energy dissipation. This behavior is attributed to the activation of the inclusions negative stiffness region, amplifying local strain and enhancing damping performance. The findings highlight the metamaterial's ability to provide tailored damping properties through pre-strain tuning.
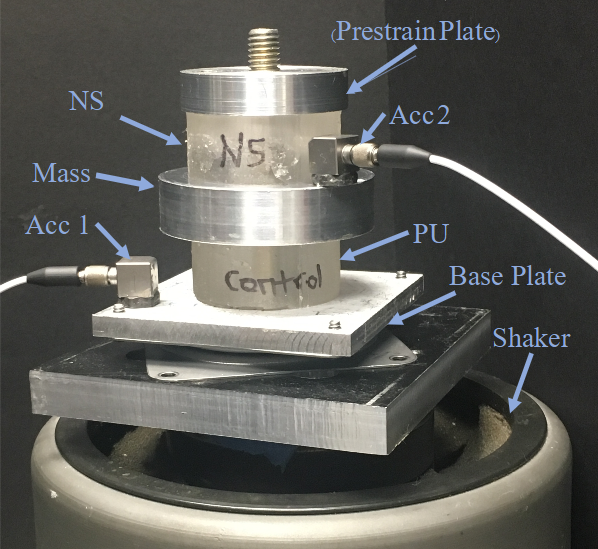
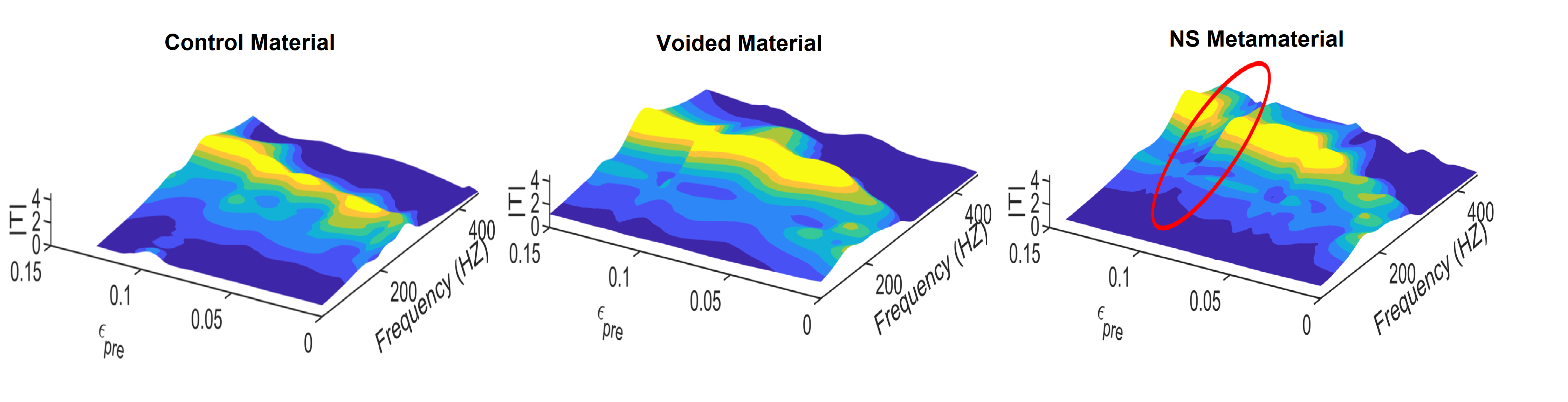
At a precise prestrain (red circle) the transmissibility of the NS metamaterial is significantly lower.